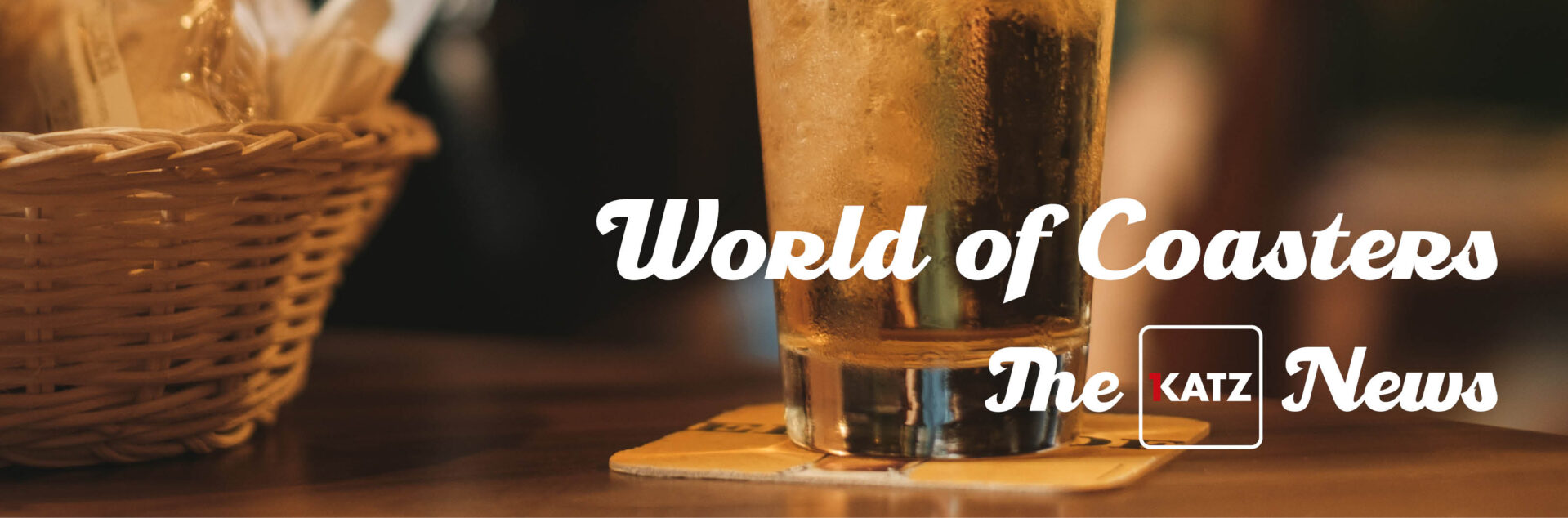
Newsletter #2 | A peek behind the scenes: How to make a beverage coaster
Station 2: Debarking
This series of articles, titled “How to make a beverage coaster,” sees us answer the following question: How are coasters actually made? In step number two, wood leaving the lumberyard goes through a debarking step in which bark is removed.
Wood from thinning: sustainable premium quality
When making our groundwood pulp coasters, we make sure to only use wood from certified and controlled sources in our region. Not only that, but the category of wood we use is known as pulpwood, which should immediately give readers a clue as to its use. This type of wood needs to be fresh, have the right moisture content, and be correctly sized.
During debarking, wood is first shortened from a length of two meters to one meter. After this, its bark is removed in a large drum (12 meters long, 5 meters in diameter), which rotates at a speed of six revolutions per minute. Ultimately, the goal is to completely remove the bark from the wood so as to prevent unattractive dark spots in the board products we make. As for the debarked logs themselves, they are then taken to our woodyard, where they can be stored until the next production step comes in.
While we’re on the subject: Myths and facts about wood and paper
Is this wood harvested specifically for making board products? No. Instead, thinning involves the selective removal of weaker trees from existing forests, which helps improve the health and growth rate of the remaining trees. How does this work? Easy: It ensures that stronger trees will have the space, light, and nutrients they need. This not only increases the corresponding productivity per unit area, but also helps sequester more CO2 from the atmosphere. As for us, the pulpwood we use consists of the thinner (weaker) log segments from the wood harvested during thinning, while segments with a larger diameter end up as sawlogs at sawmills.
If you missed station 1 of the article series “How to make a beverage coaster”, click here
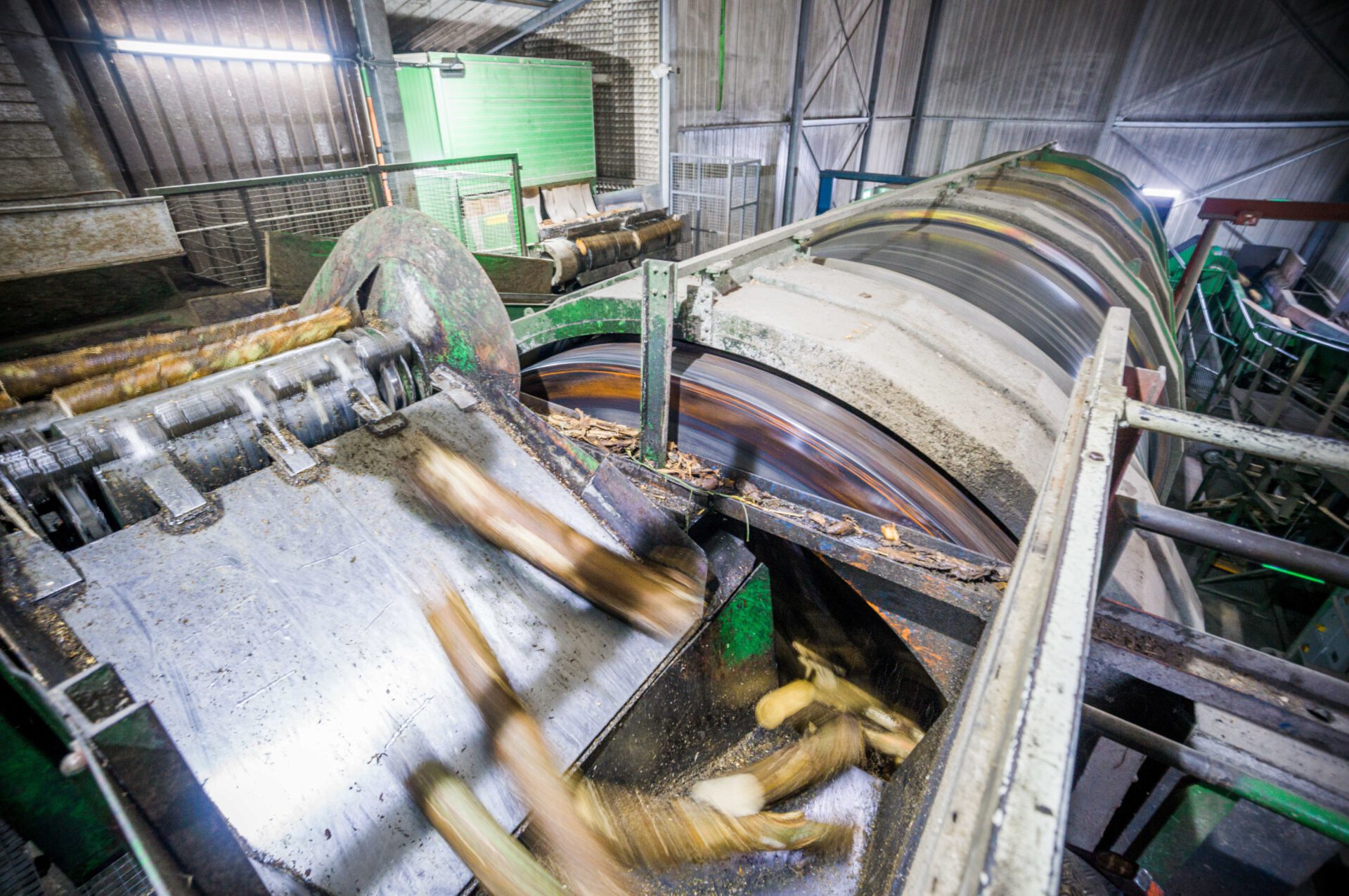
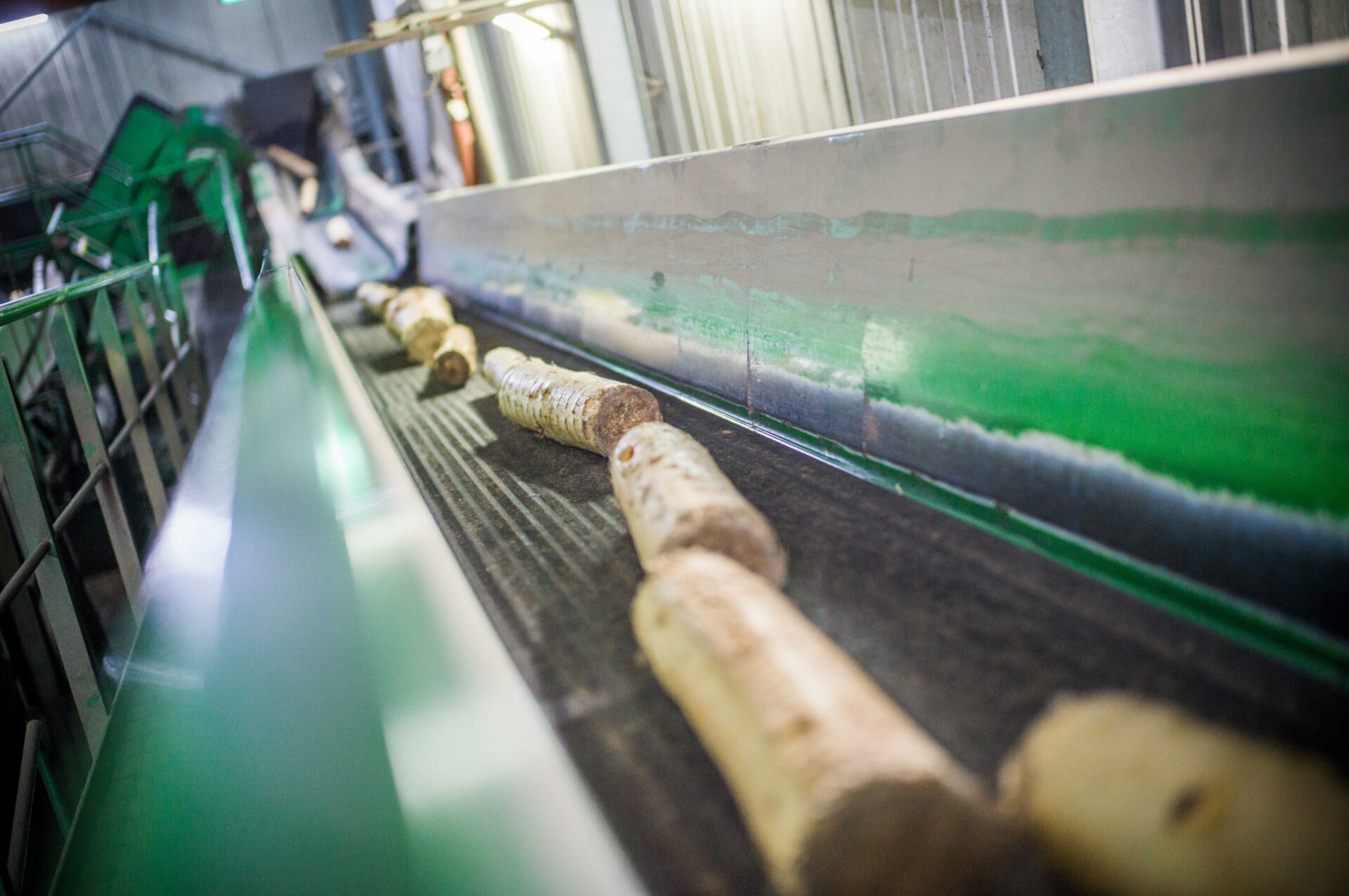