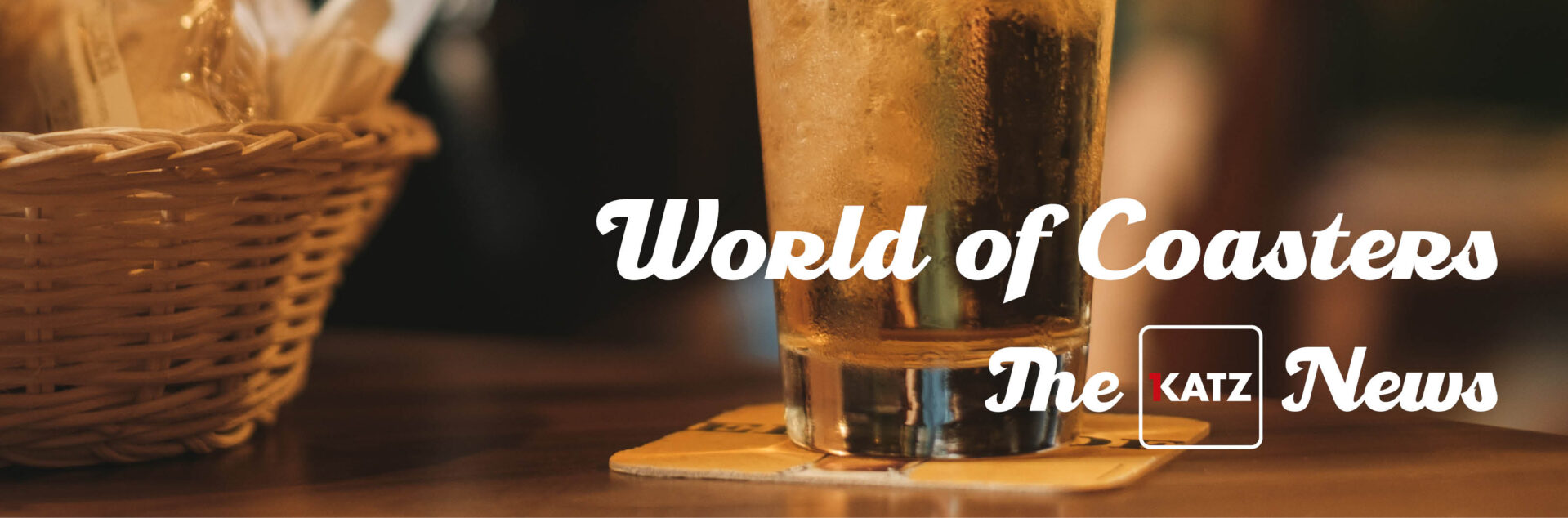
Newsletter #3 | A peek behind the scenes: How to make a beverage coaster
Station 3: Grinding
This series of articles, titled “How to make a beverage coaster,” sees us answer the following question: How are coasters actually made? After debarking comes grinding, in which debarked wood is finely ground with a rotating grinding stone – the namesake of the groundwood pulp that we use to make our wood pulp board.
Groundwood pulp: The basis of wood pulp board
Debarking gives us wood with a length of one meter and no bark that is stored at our woodyard before being conveyed into a grinding station chute with a conveyor belt. Once the logs get there, we use feed chains to push them down against the grinding stone. At that point, it’s important to make sure that the wood is parallel to the grinding stone in the chute so that it will be ground in the direction of the fibers. The result of finely grinding wood this way? Pulp.
Ultimately, the goal of this production step is to get the stock we need for processing. In fact, we also process screenings in our hammer mill until the stock is fine enough to be used in our production operations.
This step enables us to get the groundwood pulp quality we need with a very high specific volume, which is something that would be impossible to achieve with wastepaper or chemical pulp, for example. In other words, that’s what makes this production step so special.
If you missed station 2 of the article series “How to make a beverage coaster”, click here
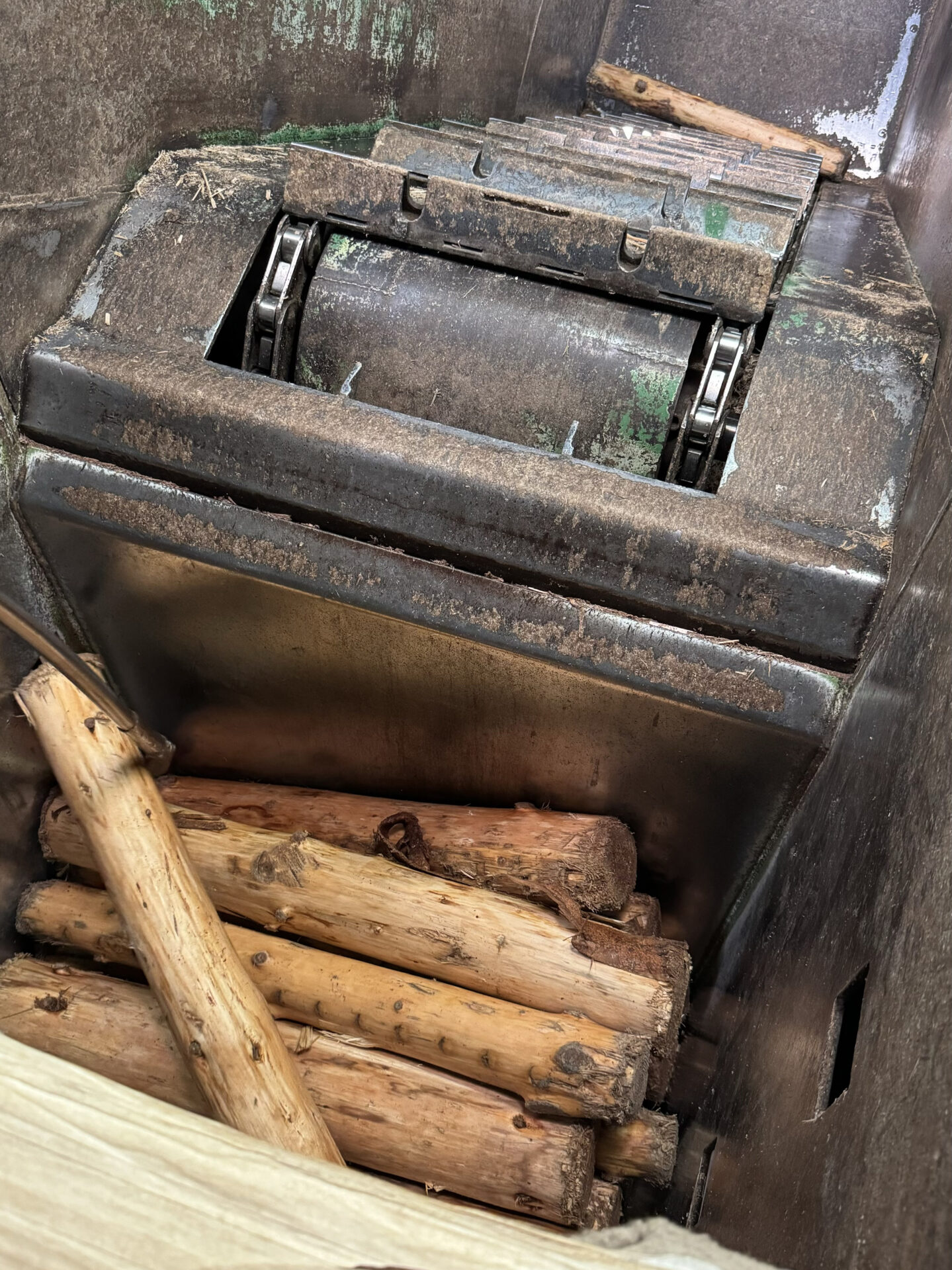